DC-PEM "Development of Cost-Effective Electrodes for PEM Water Electrolysis"
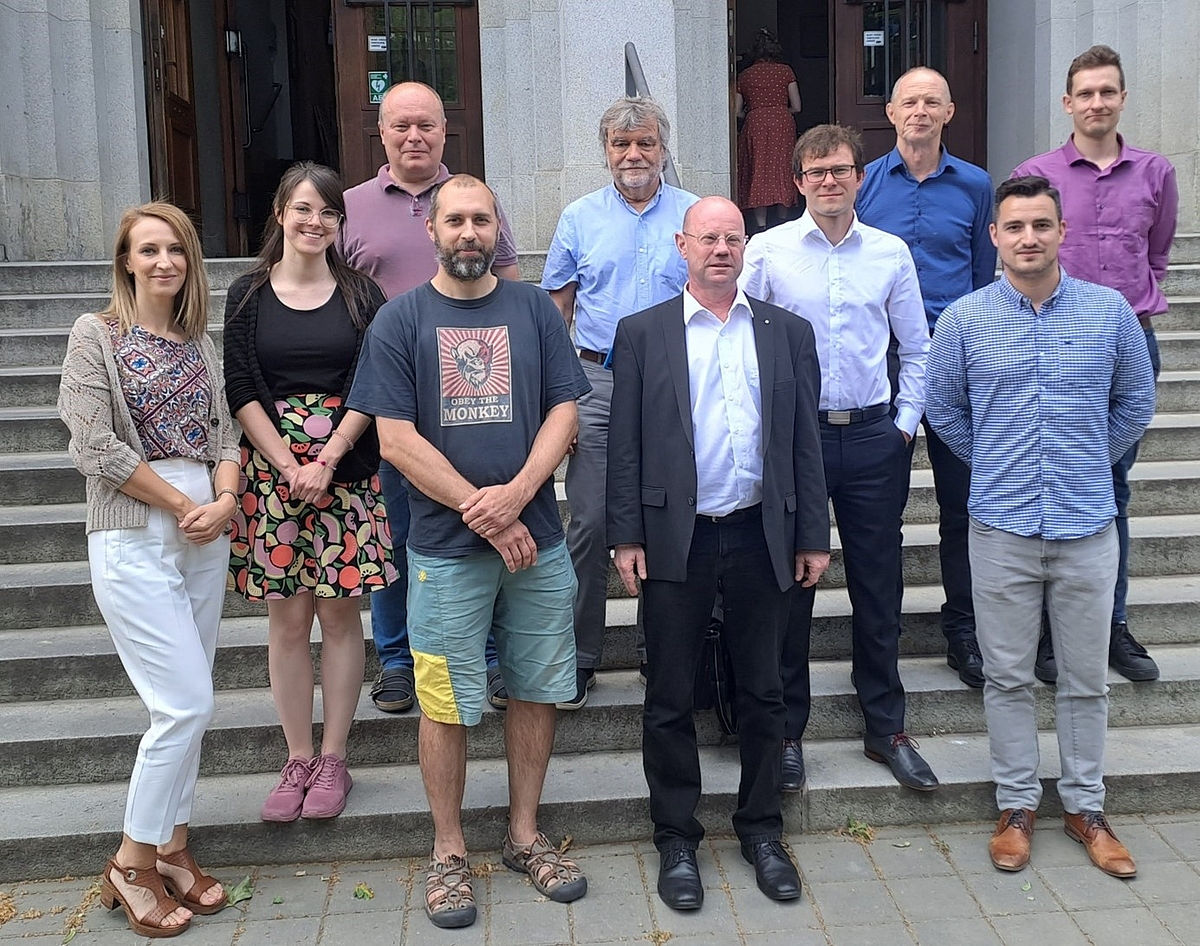
Development of a Cost-effective anode for PEM water electrolysis
Continuous development of electrolysis processes is necessary in order to efficiently store renewable energies as hydrogen over the long term. PEM electrolysis is to be addressed in this research project. The aim is the development of a scalable production route for the electrodes to reduce the production costs for electrolysers. At the same time, a recycling concept for processing the metals used is to be developed. Three research institutes and one industrial partner are working on this project to meet the specific requirements of each process step in the production and characterization of PEM electrodes.
The EU Green Deal can be summed up with the promise to become the first climate-neutral continent. In the intended project, important modules can be developed to accomplish this goal. One cornerstone for achieving a sustainable energy economy will be the development of efficient and competitive storage systems. Green hydrogen represents a versatile energy carrier that can be used as an alternative fuel or as a reducing agent in the production of green steel. Polymer Electrolyte Membrane water electrolysis (PEMWE) is already a suitable tool for the production of pure hydrogen as energy storage. In the project, various components of existing systems will be optimized in order to enable the implementation of a cost-effective and sustainable production process. The main challenge in advancing acidic water electrolysis is to improve the anode, i.e. the oxygen electrode. Due to the slow reaction kinetics, the oxygen evolution reaction (OER) is the limiting partial reaction in the splitting of water into hydrogen and oxygen. This issue is addressed by using noble metal catalysts with high activity for the OER such as iridium or ruthenium. In addition to the catalytic properties, the corrosion resistance of the materials used is also decisive for the longevity of the electrolyzers. The acidic process media and the high anodic potentials make the use of noble metals mandatory. In the project, the use of precious metals at the anode is to be reduced by improving the catalyst application. The distribution of the catalyst on the surfaces is the key factor in generating a lower electrode loading without compromising performance. Pulse plating technology will be used to generate nanoscale iridium particles on the electrodes. To ensure sustainability when using these raw materials, the project proposes a recycling concept for the electrochemical separation of the precious metals from the rest of the stack after the end of their service life. Titanium is used as the current distributor on the anode side. According to the current state of the art, fine fluxes, meshes, or sintered components are used. The disadvantages are particularly high manufacturing costs, large manufacturing tolerances, and the thickness of the base bodies. The further development of highly filled special papers based on titanium fillers envisaged in the project represents a promising possibility for the large-scale production of titanium current distributors, whereby the manufacturing costs of the stack can be significantly reduced. For the long-term stability of electrolysis, corrosion resistance plays a decisive role in the evaluation of the electrode assembly. As an alternative to precious metal coatings (with platinum or gold), the hydridation of the titanium bodies is to take place before loading with catalyst particles. The formation of titanium hydrides has technical advantages in addition to cost savings. The hydrides are excellent electron conductors, so conductivity is maintained. In the subsequent process step, the reducing properties can be used for the electrochemical immobilization of the catalyst particles. The central component of the project will be the characterization of the fabricated electrodes in terms of corrosion properties and activity for OER. The consortium will also be able to realize a complete membrane-electrode-assembly (MEA) test rig and thus investigate the performance of the developed electrodes in the cell as well as the long-term stability. The DC-PEM project covers the value chain TRL2 to TRL5 and brings together four R&D organizations and one SME, with different R&D skills and knowledge. The partners ideally complement each other in terms of technical expertise to develop, manufacture and test cost-effective anodes for PEM water electrolysis. Thus, the results of the DC-PEM project can make an important contribution to the economical synthesis and storage of green hydrogen from renewable energies.
In order to ensure a reliable starting point and good comparability of our scientific work, we have agreed on mandatory test protocols for characterizing the electrodes with regard to corrosion behaviour and electrochemical activity.
The test protocols can be downloaded here as a PDF:
Report 1 - WP1 - Technical requirements and testing protocols (PDF)